Corporate Regulatory Compliance and Quality Assurance
In order to have patients and healthcare professionals use our products with peace of mind, complying with the Act on Securing Quality, Efficacy and Safety of Products including Pharmaceuticals and Medical Devices (hereafter, Pharmaceuticals and Medical Devices Act) as well as ministerial ordnances and guidelines related to GLP*1, GCP*2, GMP*3, GQP*4, GVP*5, GPSP*6 and GDP*7, Sumitomo Pharma makes efforts to maintain and enhance the corporate regulatory compliance and quality assurance system by auditing work procedures in research, development and post-marketing activities to ensure reliability. Also, through collecting and centrally managing information obtained from patients and healthcare professionals and preventing problems through providing information on proper use, we are proactive in predictive and preventive activities.
- *1GLP (Good Laboratory Practice): Standards for Non-Clinical Studies Concerning Safety of Pharmaceuticals
- *2GCP (Good Clinical Practice): Standards for Clinical Studies of Pharmaceuticals
- *3GMP (Good Manufacturing Practice): Standards for Manufacturing control and Quality control of Pharmaceuticals and Quasi-Pharmaceutical Products
- *4GQP (Good Quality Practice): Standards for Quality Assurance for Pharmaceuticals, Quasi-Pharmaceutical Products, Cosmetics and Medical devices
- *5GVP (Good Vigilance Practice): Standards for Managing Post-marketing Safety of Pharmaceuticals, Quasi-Pharmaceutical Products, Cosmetics, Medical devices and Regenerative medicine products
- *6GPSP (Good Post-marketing Study Practice): Standards for Post-marketing Surveillance and Testing of Pharmaceuticals
- *7GDP (Good Distribution Practice): Standards for proper Distribution of Pharmaceuticals
Corporate Regulatory Compliance and Quality Assurance System
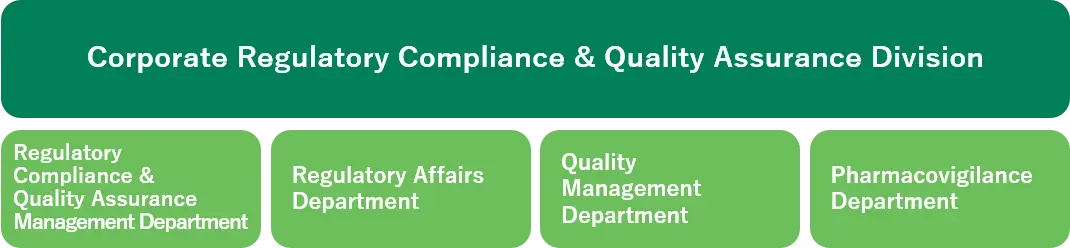
Ensuring Propriety and Data Integrity in Quality Assurance and Regulatory Affairs
For a pharmaceutical company, the integrity (completeness, consistency, accuracy) of research and manufacturing data is very important because it is the basis of the reliability of pharmaceuticals. We have systemized the recording, verification, approval and storage of data and have established and operate appropriate internal control systems.
Prevention of Harmful Incident Concerning Pharmaceuticals
We are a party to the harmful incident concerning chloroquine and
thalidomide.
Chloroquine preparations were sold in Japan for around 20 years from the 1950s to the 1970s
and were manufactured and sold by Sumitomo Chemical Co., Ltd. and Inabata & Co., Ltd. at the time.
Chloroquine was originally an anti-malaria drug. However, in Japan, the number of people suffering from
chloroquine retinopathy due to long-term administration of the drug greatly increased when the indications
were expanded to include nephritis, chronic rheumatoid arthritis, bronchial asthma and epilepsy based on scant
scientific evidence.
As for harmful incident concerning thalidomide, the administration of a thalidomide
preparation that the former Dainippon Pharmaceuticals had launched as a hypnotic and sedative for pregnant
women resulted in the births of a large number of children with thalidomide embryonic disease, a congenital
disorder affecting parts of the body such as the arms, ears and internal organs. In 1974, the Japanese
government and our company signed a confirmatory document for reconciliation with the victims based on the
premise of accepting causality and responsibility. Based on this document, the Japanese government and our
company paid compensation to all families who suffered. In addition, we have been implementing various welfare
policies for them via a thalidomide victims welfare center.
Also, to impress upon all officers and
employees that harmful incident concerning pharmaceuticals must never happen again, we carry out training
sessions for all officers and employees on harmful incident concerning pharmaceuticals and safety information
collection procedures once a year.
Establishment of a Global Quality Assurance System for Delivering "A-N-SHI-N"
In order to ensure a high level of quality in the production of pharmaceuticals, strict GMP standards have been established in each country. The Sumitomo Pharma Group is developing new drugs in Japan, the U.S., China, and other countries, after receiving rigorous review and approval from each country's regulatory authority, such as Japan's Ministry of Health, Labour and Welfare, the U.S. Food and Drug Administration (FDA), the European Medicines Agency (EMA), and Australia's Therapeutic Goods Administration (TGA), delivering products. The pharmaceutical products are manufactured at plants with high level facility designs and quality assurance systems that have fulfilled audit requirements by overseas partner companies and meet strict quality standards at global level, such as guidelines from the International Council for Harmonisation of Technical Requirements for Pharmaceuticals for Human Use (ICH).
In order to provide products that patients and healthcare professionals from around the world can use with "A-N-SHI-N"*8, our Group has established a Global Quality Policy*9, for quality and safety management, which is applicable to all group companies. Under a Global Corporate Regulatory Compliance System, we are striving to provide high quality products.
- *8A-N-SHI-N: Trustworthiness, reliability, peace of mind, making people feel reassured and safe
- *9SMP GROUP QUALITY POLICY
Furthermore, we supervise all manufacturing and packaging contractors for our pharmaceutical products in various countries to assure quality across the entire supply chain. This approach to quality assurance activities, from development to post-marketing services, is implemented under a framework unifying our Group.
Prompt Inquiry-response with Our Quality Information System
In Japan, our Quality Information System is designed to ensure prompt responses to inquiries about product quality from healthcare professionals. We use this system in conformity to GQP.
When an inquiry raised in the system, the plant at which the product was manufactured begins investigating immediately, checking retained samples from the same lot, verifying manufacturing records and confirming the quality of the product in question. The root cause of the quality issue is also investigated, and when necessary, the plant plans and implements actions to prevent recurrence.
Members of departments such as Quality Assurance, Sales & Marketing, Manufacturing, and Pharmacovigilance can access the system so that they can promptly evaluate safety and respond to complaints. Our Quality Information System also has a search function which enables us to analyze inquiry and quality issue trends per each product type and time period to prevent similar problems in the future. In addition, our medical representatives (MRs) carry tablet devices that have answers to frequently asked inquiries. This has made it possible for them to provide faster responses to inquiries from healthcare professionals.
Centralized Management of Safety Information and Timely Implementation of Safety Measures in Pharmacovigilance
Centralized Management of Safety Information from Development to Post-marketing
Adverse reactions that were unexpected during the development stage can occur once
pharmaceuticals have started to be used by a large number of patients under various conditions after
manufacturing and marketing approval. Because of this, we collect a wide range of post-marketing information
from medical institutions, partner companies, and other sources, in addition to safety information collected
from the early development stages.
A centralized global database manages and evaluate safety information
collected in Japan and overseas, leading to the planning of necessary measures to ensure the safety and proper
use of pharmaceuticals and their implementation of safety measures in a timely manner. These safety management
activities are in compliance with the Pharmaceuticals and Medical Devices Act and GVP. At the time of
approval, we draw up a pharmaceutical risk management plan (RMP) and as part of the pharmacovigilance activity
based on the RMP, we carry out post-marketing surveillance in compliance with GPSP as required.
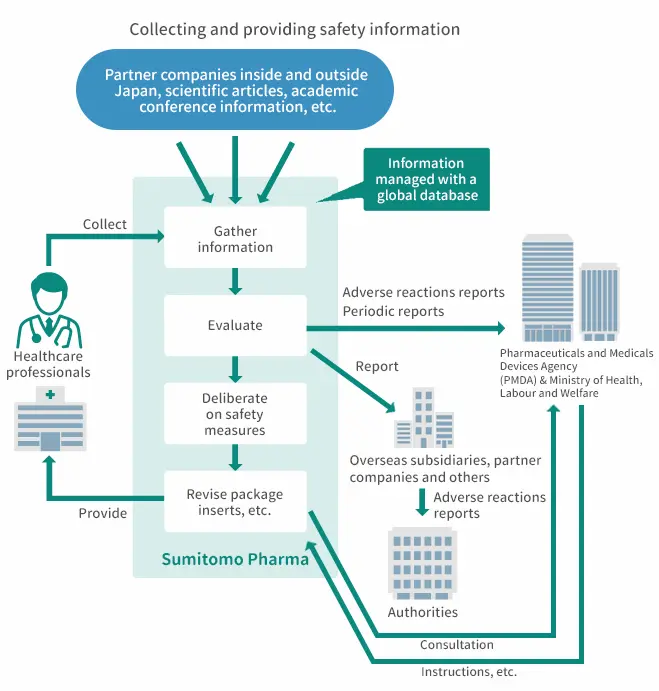
In order to provide products that patients and healthcare professionals around the world can use with "A-N-SHI-N", the Group has established a Global Safety Policy*10 for all group companies and endeavors to provide safety information to ensure their proper use under a global corporate regulatory compliance and quality assurance system.
Promoting Proper Use through Appropriate Provision of Information
Providing Easy-to-understand Information to Support Proper Use
While pharmaceutical products are effective when used properly, their improper use can
not only negate their effects, but can also lead to occur undesired effects.
We promptly and accurately provide healthcare professionals with information on the proper use of
pharmaceuticals in order to ensure that the effects of each pharmaceutical can be produced more safely for
patients. For example, when new adverse reactions are added to electronic package inserts, a Drug Safety
Update (DSU) is promptly provided to prescribing physicians and pharmacists by MRs and via our website for
healthcare professionals.
As part of our commitment to promoting the proper use of our products, we develop and provide a range of
materials for healthcare professionals. These include the RMP and other resources designed to support
appropriate clinical use. We also produce patient-oriented materials, such as “Kusuri-no-shiori”, (drug
information sheets) and “Drug Guides for Patients,” to assist healthcare professionals in explaining
medication usage and specific symptoms of potential adverse reactions to patients. These materials are made
available through our MRs and our corporate website.
We will continue to utilize our website and other communication channels to deliver clear, accessible
information that meets the evolving needs of patients, their families, and healthcare professionals.
Product Information System
In addition to providing information through our corporate website, we strive to respond to inquiries from healthcare professionals regarding our products with prompt and accurate information delivered by our MRs and Product Information Center, utilizing our in-house product information system. We are committed to continuously reviewing and enriching our content to better reflect the needs of healthcare professionals, with the aim of enhancing the reliability of the information we provide and contributing to greater customer satisfaction.
Act as an Information Hub Further Utilizing Customer Feedback
As a contact point related to our products, we have established the "Product Information Center" to respond to inquiries from patients, their families, and healthcare professionals. We aim to continue providing prompt, accurate, and courteous information on proper usage, contributing to the well-being of patients. Additionally, we will strengthen our role of analyzing customer feedback obtained through inquiry responses, appropriately relaying it within the organization, and visualizing trends in customer feedback to drive improvements.
Total number of inquiries in fiscal 2024 (April 1, 2024 - March 31, 2025) was approximately 21,700.
For more information on the Product Information Center including total numbers of inquiries received, please see “ESG Data Table.”
Creation of New Drugs Needed by Patients
As a research and development-oriented pharmaceutical company with a global presence, Sumitomo Pharma aims to create innovative and valuable pharmaceutical products targeting therapeutic areas, particularly those with high unmet needs (for both healthcare professionals and patients).
For more information on Research and Development, please see "Research and Development.”
For more information on Responding to Demands for Development of Unapproved or Off-Label Drugs, please see “Initiatives to Improve Access to Medicines.”
At Sumitomo Pharma, the safety of the patients who use our products is a top priority. To ensure their safety, we incorporate the dosage forms and indications that best meet patients' needs from the initial planning stages of development, as well as we strive to prevent medical errors by making products more distinguishable and by distributing notices for precaution.
Prevention of Medical Malpractice
There are many restrictions on the packaging and labeling of pharmaceuticals,
including the requirement to present information prescribed by law. This has resulted in similar package
designs by different pharmaceutical companies, which is a contributing factor in pharmaceutical product
mix-ups.
At Sumitomo Pharma, the Supply Chain Division leads our efforts to respond to the needs of both
medical institutions and patients by improving packaging and label designs to prevent medical errors. We focus
particularly closely on making sure that our packaging and labels are easily distinguished from other products
since serious problems can arise when pharmaceuticals are taken incorrectly. Although we check in advance to
ensure that our product names and package designs are not similar to products already on the market, we take
immediate action to rectify the situation when our products are mistaken for others despite these efforts. We
work with the company relevant to the marketing of products to modify product names and designs so that they
are easily distinguishable from one another.
Printing of the Press-through Package (PTP)
To make our products more distinguishable, we have addressed product safety measures by expanding the usage of a special printing process for the PTP. By printing the name and dosage on the PTP sheets for each tablet, we aim to prevent mix-ups when individual tablets are separated from the sheets.
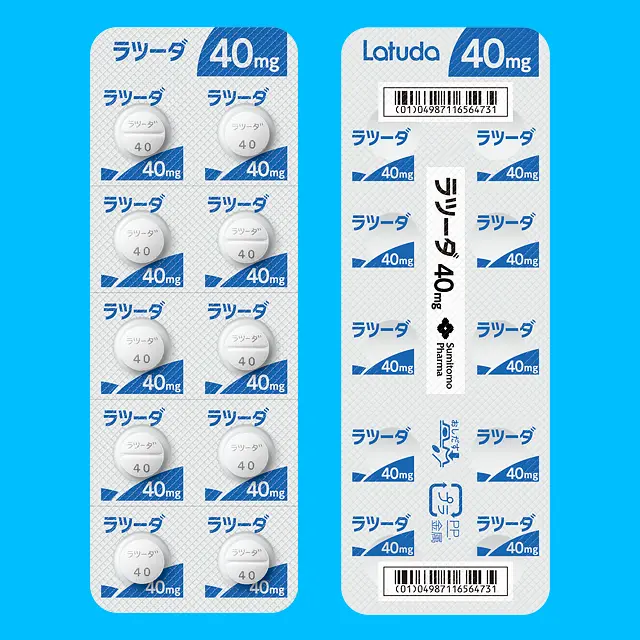
Printing Product Names on the Top of the Lids of Bottle Containers
As a means of preventing mix-ups in the by medical institutions and patients, we
are
working to implement such steps as printing product names on top of the lids of bottle container and
introducing packaging and labeling designs that are highly identifiable.
We introduced the industry's
first laser printing to our manufacturing line in order to print the product name on the top of the
bottle-cap
containing our tablets. Since most medical institutions store these bottles in drawers, having the product
name printed on the cap, as well as on the bottle, makes products easier to identify and retrieve.
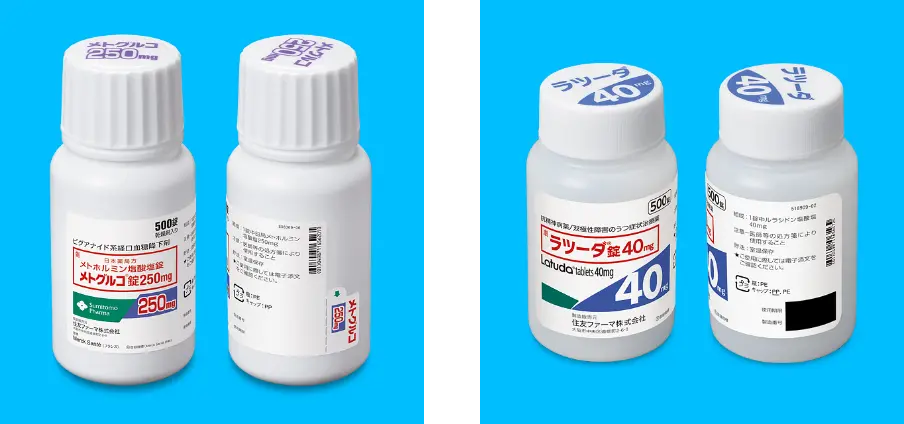
Information Card Specification for Product Boxes
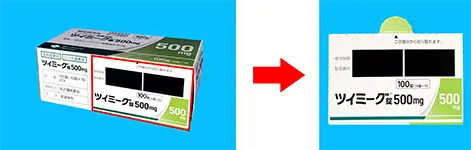
The information card specification for product boxes means that the product information on the side of the box may be easily peeled off. The product information on the peeled off card can be kept together with the PTP sheet in a drawer of the dispensing shelf. Keeping required product information together with the PTP sheet aids inventory management.